UPEG Develops Turbine Combustor for Burning Orimulsion
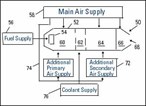
Ultimate Power Engineering Group's (UPEG) Rich-Quench-Lean Combustor is the first combustor that will permit the burning of orimulsion and other fuels having high vanadium contents in gas turbine systems. The Rich-Quench-Lean Combustor is a multi-zone combustor with injection ports and exhaust-gas temperature controls. Prior to the introduction of this combustor, orimulsion and other vanadium-rich fuels could not be used in gas turbines because of the buildup and corrosion of vanadium pentoxide (V2O5).
In a conventional gas turbine, the burning of high vanadium fuels like orimulsion would create V2O5 inside the turbine. The gummy, sticky byproduct is not present when the fuel is in a liquid state. Rather, the corrosive substance is produced when the liquid fuel is burned. V2O5 deposits foul combustors, clog air passages, and collect on rotating blades and stationary blades or vanes. Depending on the vanadium content in the fuel, this buildup can occur over a matter of hours and will eventually force the turbine to shut down. The new combustor solves the problems created by V2O5 deposits by converting the V2O5 into Vanadium Tetroxide (V2O4) / (V2O3) in a high melting form.
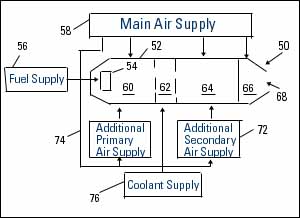
In the drawings above and below, figures 1 and 2, a burner inside the shell of a can-type combustor receives fuel contaminated with vanadium. A main air supply (such as a reservoir of air from a compressor) injects air into the combustor, but not enough for complete combustion of the fuel. This permits an additional primary air supply and an additional secondary air supply to be controlled so that the rate at which they inject air determines the stoichiometric conditions in a primary combustion zone and a secondary combustion zone inside the combustor. The additional primary and secondary air supplies receive their air from the main air supply and control the injection rate with valves as shown in figure 3.
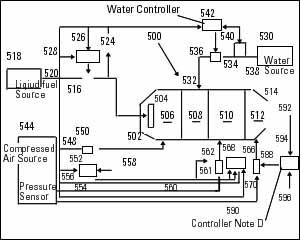
The fuel is burned rich in the primary combustion zone, so that considerable unburned carbon and carbon monoxide remain and create a chemically reducing environment in the primary combustion zone. A study shows that this favors the conversion of any vanadium that may be present in the fuel to powdery V2O3 and V2O4 rather than gummy V2O5. Water from a coolant supply is injected between the primary and secondary combustion zones to form a quenching zone between them.
The hot gasses and unburned fuel from the primary combustion zone undergo a rapid temperature drop in the quenching zone, and study show that this converts any V2O5 that has formed along with the V2O3 and V2O4 in the primary combustion zone into more V2O3 and V2O4.
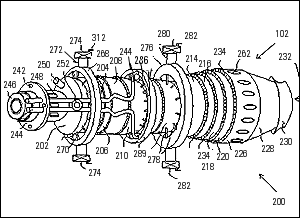
The gas leaving the quenching zone is still hot enough to spontaneously ignite the unburned carbon when the gas reaches the secondary combustion zone. The carbon is burned under slightly lean conditions in the secondary combustion zone, raising the temperature of the gas again. In the mixing zone following the secondary combustion zone, air from the main air supply is mixed with the hot gas to control the exhaust temperature and avoid temperature stratification of the exhaust gas (which is laden with V2O3 and V2O4 but not V2O5).
UPEG received patent 5,819,540 from United States Patent and Trademark Office (USPTO) this week for the Rich-Quench-Lean Combustor. Currently UPEG has confidentiality agreements with three combustion turbine manufacturers, and several oil companies. According to Ultimate Power Engineering Group president Madhat Massarani, "the company is interested in seeking a partner to licensing the technology and further the development of the system for commercial applications in power generation." Still, the combustor is now available to power producers with a 12 to 16 month lead-time.
Another interesting feature of the combustor is that it can also fire oil, natural gas, methane, diesel, fuel-oil, and kerosene. While this dual-fuel combustor will not fire coal in any form, it does have the ability to swap fuel inputs while firing. The combustor is equipped with sensors that use fuzzy logic controllers. This system permits users to switch from orimulsion to methane or any other fuel without shutting the unit down. Sensors also autodetect oxygen content, CO content, and CO2 content in the fuel and adjust the combustor for optimum combustion. Burning orimulsion is like burning coal in a liquid state, but has fewer NOX, CO, CO2, and sulfur emissions than coal. When the combustor is burning orimulsion the emissions are well within the federal regulated guidelines. When combustor burns conventional fuels the emissions are cleaner than those produced by conventional combustors. This is because the dual zone firing produces fewer emissions, especially NOX.
Orimulsion and other high vanadium petroleum reserves are both cheap and abundant. Reserves that lay idle in places like the belt of Venezuela can now be exploited economically. Currently, Venezuela has the patent on the process used to turn orimulsion it into a liquid fuel.
Use of this new combustor and gas turbine could substantially lower the cost of electricity in some regions of the world due to cheaper fuel costs. Orimulsion has the highest vanadium content of all fuels; between 370 PPM and 420 PPM. With this new combustor, orimulsion can be directly burned in combustion turbines for the first time. In addition, this system can be used in both simple cycle and combine cycle designs, furthering efficiency. Further, the combustor can be easily modified to handle boiler applications. On the boiler application, there is two-stage combustor, but this second stage is only used with a boiler
Combustion turbine manufactures currently have a limit on vanadium content of 5 PPM for their equipment. Some plants are running up to 90 PPM but they are having problems, they use magnesium-based additives in a ratio of three parts magnesium to one part vanadium to reduce the firing temperature to produce less V205. The higher the temperature the more v205 produced. They also derate the turbines when they reduce these firing temperatures. A 100 MW turbine might be rated as 85 MW. The main advantage of the Rich-Quench-Lean Combustor design is that it can burn heavy fuels with a content of vanadium up to 500 PPM. No other combustors currently available can burn this fuel without modification.
The maintenance of the unit basically follows the same guidelines for any standard combustor in terms of hours between inspections, scheduled teardowns, etc. It also has a computer to inform technicians and operators about mechanical problems. This has an advantage over many conventional combustors that need to be opened up to diagnose problems.
The unit, which took five years to develop, is comparable in cost with conventional combustors, particularly when fuel saving are figured into the overall cost structure. The combustor also compares in size to conventional combustors and uses standard combustion turbine openings for installation. Intended for new and retrofit applications, likely users would include IPPs and utilities that want to upgrade their boiler applications. However, most of the orders will probably come from the Pacific Rim, South America, and the Middle East, as this is where most of the high-vanadium fuel is found.
For more information contact Utimate Power Engineering Group at P.O. Box 1461, Lombard, IL, 60148; Tel: 630-629-0401.