Turbomachinery Symposium: Conax demos temperature sensors for gas turbines
Conax Buffalo Technologies (Buffalo, NY) rolled out its latest line of temperature sensors for ground-based power generation turbines at the Texas A&M Turbomachinery Laboratory's Turbomachinery Symposium in Houston this week.
Conax designed its Fiber Optic Temperature Sensor System—the centerpiece of its symposium display—specifically for advanced gas turbines, said Richard A. Lyon, product manager for Conax.
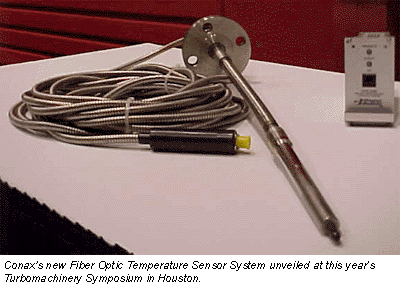
According to Lyon, Conax designed the system to replace conventional thermocouples subjected to high velocity, high temperature gas flows to improve sensor reliablity, measurement accuracy and life expectancy—all crucial to power plant operators facing tighter budgets and more competition.
Conax's new optical sensor operates directly in the turbine inlet, distinguishing it from traditional thermocouple technology that measures exhaust gas temperature. This, Lyon said, gives operators more accurate measurements that provide a longer "heads up," or lead time, allowing them to make adjustments earlier in the generation process to increase efficiency and lower emissions.
"Taking measurements as the exhaust leaves the plant, doesn't give you a whole lot of control," Lyon said. "And with today's emphasis on emissions, you want to have as much control of what comes out that stack as possible."
Efficiency and power output improvements in gas turbine systems produce increases in turbine inlet temperatures to well over 10000C for base load operation.
At such elevated temperatures and in gas flow velocities of up to Mach 0.9, Lyon said, a five-year trial program of Conax's new system with a major manufacturer and an American utility revealed it can deliver superior measurements for turbine inlet and inter-turbine temperatures.
Features of the Fiber Optic Temperature System:
- A silicon carbide sheath housed in a super-alloy well provides protection for the sapphire sensor. Lyon said this material selection and housing design provide reliable performance at turbine inlet locations.
- The flexible design of the shaft accommodates the thermal expansion normally encountered during turbine operation between the hot gas path and the turbine housing.
- Mounting configurations are designed to fit virtually any turbine system interface. Sensor probe lengths can be varied to accommodate turbine frames.
- The optical path integrates with the electro-optical unit (EOU), forming a closed loop system.
- Conax designed the rugged termination head specifically for the power plant environment.
- Double-linked superflex stainless steel armor cable provides optical cable protection.
- The EOU separates the optical signal into two separate wavelength bands, amplifies the signals and converts to digital values. The EOU remains permanently attached to each probe and stores information specific to that probe's operation. Also, Lyon said, this calibration information downloads to the signal processor when a new probe is installed, limiting reprogramming.
- Digital signals from the EOU transfer to the digital signal processor via an RS-485 interface. The output signal is based on the signal levels and calibration information that the digital signal processor receives from the EOU. And the digital signal processor can be configured for a variety of output signal schemes.
For more information about Conax's Fiber Optic Temperature Sensor System or its line of thermocouple and RTD sensors, and sealing assemblies for sealing bearing sensor wires and probes, contact 800-223-2389, fax 716-684-7433, conaxbuf@conaxbuffalo.com, or visit www.conaxbuffalo.com.
By April C. Murelio
Managing Editor, Power Online