The Cansolv System Process: A new paradigm for SO 2 recovery and recycle (Part II)

By John N. Sarlis and Patrick M. Ravary
Cansolv Technologies Inc.
8475, avenue Christophe-Colomb, Suite 2000
Montreal, Quebec, H2M 2N9 Canada
http://www.cansolv.com
The Cansolv System is an aqueous amine-based regenerative gas desulfurization process that promises SO2 removal down to a few ppm. The first section of this paper looks at process technology. The second section explores potential uses in sulfuric acid plants, spent acid recovery plants, sulfide ore smelters, sulfur recovery units, flue gas desulfurization units, pulp mills, and SO2 production, storage, and transportation.
Contents
Smelter/acid plants
Smelters
Refinery/natural gas
Sulfite Pulp Mills
Safe SO2 Storage and Transport
Pilot testing
Gas stream conditions
Test results
Conclusions
The Cansolv System can be applied to sulfuric acid manufacture, spent acid recovery plants, sulfide ore smelters, sulfur recovery units, SO2 production and safe storage and transportation, flue gas desulfurization units and pulp mills. Details of these applications can be found in other Cansolv Technologies Inc. (CTI) publications as well as in CTI's Web site (http://www.cansolv.com). The following paragraphs summarize the application of the Cansolv System in various industrial and utility markets.
Smelter/acid plants(Back to Top)
The two largest sources of sulfuric acid are sulfur-burning acid plants, which produce on-purpose or voluntary acid, and sulfide ore smelters, where the acid is the byproduct of emission control. In both cases, conventional contact acid plants are used. Most acid plants built in the last 25 years are of the double absorption design illustrated in Figure 2, which emit a tail gas containing generally less than 500 ppm SO2 into the atmosphere. The older single absorption plants produce a tailgas with up to 3000 ppm SO2. Thus, while considerable improvement has occurred in air emissions, continuing environmental and cost reduction pressure is driving the search for more effective and efficient technologies.
In sulfide ore smelters, the adoption of oxygen based roasting has produced substantial decreases in total emission levels and improvements in the capture of fugitive emissions has improved plant industrial hygiene and pollution performance. However, considerable room for improvement remains, particularly in the areas of improving the economics of treating low strength SO2 streams, both fugitive and primary, and in dealing with the often cyclical SO2 load on the acid plant caused by the batch operation nature of current converter designs. Weak SO2 streams introduce a high level of inerts into the acid plant, thereby requiring a larger unit to handle the gas flow, and in some cases even requiring the use of alternative technologies to control emissions. A varying SO2 feed rate prevents optimal steady state operation of the unit, resulting in increased SO2 emissions.
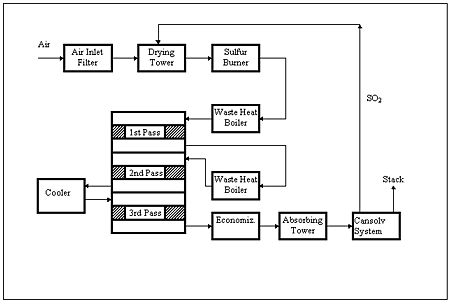
Cansolv System SO2 scrubbing technology can be used instead of a second absorption step to reduce sulfur emissions from sulfuric acid plants, as illustrated in Figure 3.
Since the capital and operating costs of the Cansolv System scrubbing unit are relatively insensitive to the concentration of SO2 in the feed gas, in many cases three contact stages are the economic optimum, as shown in Figure 3. The advantages of the Cansolv System process over a conventional second absorption stage are:
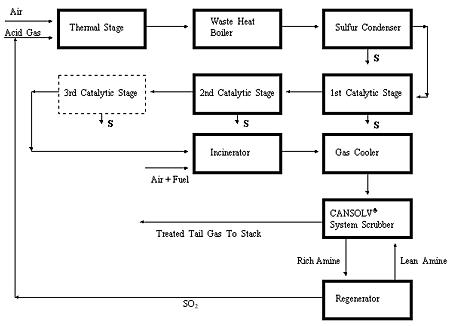
Smelters
Cansolv SO2 scrubbing technology can address this deficiency by selectively capturing the SO2 from weak streams and feeding it as a pure water saturated product to the acid plant drying tower. The inerts from these streams are rejected to stack. Very substantial savings in initial capital investment can be realized, while reducing total emissions. Alternatively, an existing sulfuric acid plant can be debottlenecked in the same manner, enabling an increased smelting rate with a very modest capital investment, since the acid plant often limits smelting rate.
Metallurgical acid plants often operate with a very cyclical inlet SO2 concentration, due to the batch operating nature of current converter designs. This has the undesirable effect of preventing the acid plant from operating in a steady state optimum manner, which tends to increase emissions. Additionally, mechanical stresses caused by thermal cycling tends to increase maintenance costs. The SO2SAFE Storage Technology can mitigate these effects by providing load-leveling capability. During peaks, SO2 is scrubbed from the acid plant feed gas and the loaded solvent is held in a buffer storage tank. At times of low SO2 concentration in the acid plant feed, rich solvent is regenerated and the SO2 is added to the acid plant feed gas. The response time constant of the Cansolv System process is of the order of one minute or less, enabling accurate load following. The optimum degree of damping the cyclicality is site specific. In the limit, complete decoupling of the smelter and acid plant can be achieved by specifying a sufficiently high rate and storage capacity for the load leveling equipment.
Finally, the use of Cansolv System flue gas desulfurization can enable the use of high sulfur, low cost fuels such as petroleum coke and heavy refinery residues in the site utility boilers or cogeneration unit. The SO2 byproduct can be converted to H2SO4 in the existing acid plant. Payback periods of 2 years or less are projected for the additional plant investment over a gas fired cogeneration unit.
Refinery/natural gas(Back to Top)
The refining industry faces three trends with serious cost increase implications. The global average crude oil is getting heavier and higher in sulfur, while regulations are requiring lower sulfur content in the products and lower emissions from the refineries. Exacerbating the situation is the shrinking market for residue fuels that in the past absorbed a substantial fraction of the crude slate sulfur content. In fact, disposition of the bottom of the barrel (very heavy residues and petroleum coke) is a growing problem for refiners.
These factors have caused refineries grow more complex, increase hydrotreating, boost sulfur recovery unit (SRU) capacity, and use cleaner fuels in an effort to reduce emissions from such major sources as SRUs, boilers, and the fluidized catalytic cracking unit (FCCU) regenerator flue gas (CO boiler flue gas). The refining industry is thus facing major capital investments, while having to deal with a very competitive marketplace for products.
Reduction of sulfur emissions from SRU's is being achieved by the application of various technologies:
The above processes reduce emissions adequately, but do increase costs significantly and some have operating constraints requiring careful control.
SRU capacity expansion, as an alternative to construction of a complete new train, is currently most often achieved by oxygen enrichment of the thermal stage combustion air. This reduces the inerts flow through the unit, making room for additional acid gas. At high levels of enrichment or with pure oxygen, extensive modifications to existing equipment must be made. The use of oxygen of course incurs a significant operating cost increase.
FCCU sulfur emission control is now practiced by primarily two technologies - the use of sulfur transfer catalysts or caustic (or soda ash) scrubbing. Costs of both control options are quite sensitive to the concentration of SO2 in the uncontrolled tail gas. The use of heavier, high-sulfur crudes and increased residue cracking are increasing emission control costs significantly. Units losing grandfathering and new FCCU's will have to bear the compliance cost.
While these and other advances in technology have helped operating companies to meet requirements, the pressures to improve environmental performance and reduce costs are unrelenting.
Cansolv System technologies offer new tools to deal with these challenges. The processes, as described below, now provide a new options for SRU tail gas treatment, debottlenecking and for new sulfur recovery units of conventional design. Cansolv also introduces a new paradigm for SRU design, due to its ability to economically, selectively and regenerably scrub SO2 from gas streams. The ability to remove SO2 from flue gas at lower cost, and to the most stringent standards, opens the door for FCCU emission control and the use of low value, high sulfur residuals and petroleum coke as refinery fuel or in cogeneration.
The following discussion is applicable to both natural gas and refinery SRU's. Refiners can take advantage of the considerable economies and operating advantages accruing from destruction of dirty feed streams containing ammonia, hydrocarbons etc. Natural gas processors with low H2S to CO2 ratios will benefit from the capital and operating cost advantages resulting from the almost complete equilibrium selectivity of the Cansolv System scrubbing process for SO2 over CO2. Conventional TGTU's can absorb large quantities of CO2 along with H2S , resulting in the recycle of inert material to the SRU.
Cansolv System TGTU. A Cansolv unit can perform sulfur removal from natural gas plant and refinery Claus unit tail gas, simply replacing a conventional TGTU, as shown in Figure 4. The major difference is that the Claus tail gas is incinerated and then scrubbed, rather than reduced and scrubbed as in conventional technology.
The Cansolv System TGTU has very significant advantages over a conventional TGTU:
Debottlenecking. Even greater benefits can be obtained by actually integrating Cansolv technology into the operation of the SRU, beyond just tail gas treatment, as is illustrated in Figure 5. In this configuration, a part of the acid gas bypasses the Claus unit and is incinerated with excess air, along with the Claus tail gas. The SO2 recycled to the Claus thermal stage reduces the combustion air requirement, thereby also reducing the process gas flow by eliminating the nitrogen inerts. This effectively unloads the SRU, allowing for increased capacity at a low incremental cost over the Cansolv System TGTU alone. The high operating cost of oxygen enrichment is avoided, while realizing in addition to the above advantages the following additional benefits:
Varying degrees of debottlenecking can be implemented by changing the amount of acid gas bypassed to the incinerator. Large capacity expansions will possibly require some modifications to the existing equipment, to deal with the higher sulfur production and heat release.
Cansolv SRU. The end point for the paradigm shift driven by incorporation of Cansolv System technology into sulfur recovery units is the "Cansolv SRU" illustrated in Figure 6. This new design paradigm is projected to have substantially lower capital cost than current designs. As can be seen by comparison to Figure 5, fewer pieces of major equipment are required, reducing cost and simplifying operation. Extremely high sulfur recoveries can be achieved in a simple, easier to operate process. Due to the rejection of inerts contained in the acid gas bypassed to the incinerator, the sulfur reactant concentrations in the feed to the catalytic stages are increased. This will push the application envelope of the Cansolv SRU process to lower H2S concentration acid gas than that treatable with conventional technology.
The operational advantages mentioned above are also obtained in the Cansolv System SRU process configuration. A further saving in this design is the lower air blower head required, because the combustion air is fed to the essentially atmospheric pressure incinerator, rather than the thermal stage of a conventional unit which operates at a pressure of 6 - 12 psig.
FGD applications. One of the principal attributes of FBC is its ability to combust most solid fuels, including low reactivity materials. Its use can be most attractive when using low cost fuels such as high sulfur coal or petroleum coke.
Combustion of such high sulfur fuels requires that an efficient desulfurization method be utilized in order to meet the increasingly stringent regulatory emission limits. Traditional methods using limestone involve the introduction and later collection and disposal of large quantities of solids.
Disposal of these solid by-products can be problematic. In certain jurisdictions the solids may be considered hazardous waste, increasing disposal costs and reducing disposal options. In those areas where waste disposal is difficult, expensive or impossible but where an economic incentive to burn low cost high sulfur fuels exits, a regenerable SO2 scrubbing technique would be advantageous, especially when this technique is cost competitive with conventional limestone scrubbing.
The Cansolv System FGD process is a regenerable SO2 scrubbing process that utilizes a solvent specific for the capture of SO2, and produces a pure SO2 byproduct. The solvent is not consumed in the process and does not contribute to the by-product stream. The cost of the scrubbing process is largely insensitive to SO2 concentration in the flue gas or the sulfur content in the fuel. Thus the highest sulfur, lowest cost fuel can be consumed, maximizing the economic benefits.
With limestone desulfurization, FBC only converts an air emission problem into a waste solids disposal problem. As much as a half-ton of waste may be generated per ton of fuel burned or ten tons per hour for the equivalent of a 50 MW boiler.
The problem is becoming more severe as the higher sulfur removal efficiencies being mandated by current legislation are forcing boiler operators to increase the ratio of limestone to fuel in their feed. This leads to greater costs and difficulty in disposing of the solid by-products, as well as a decrease in boiler efficiency.
Cansolv FGD with FBC. The use of limestone with FBC's is a proven technology for controlling SO2 emissions.
Limestone is introduced in the furnace where it is calcined to lime. The lime reacts with the SO2 released by the combustion of the fuel to form calcium sulfite and calcium sulfate. Excess limestone is added in order to increase overall SO2 capture.
The calcium sulfite/sulfate byproduct is collected with the unreacted quicklime, carbon and ash as a solid waste requiring disposal. The calcium sulfite/sulfate and residual lime can represent more than 80% of the overall solid waste collected depending on sulfur and ash content in the fuel and SO2 removal efficiency in the FBC.
The Cansolv System FGD process is an alternative to limestone FGD. Similar to conventional amine treating for H2S and CO2 scrubbing, it is a regenerable process which utilizes a water soluble amine that is highly selective to SO2. The amine, once regenerated, is reused. The SO2 recovered can be used as is, or converted to sulfur or sulfuric acid. Cansolv System FGD is a robust and easy to operate process. It consumes no chemicals and, other than the ash collected, generates virtually no additional wastes. Total emissions, to air, water and landfill are minimized.
The Cansolv process is located after the air preheater of the FBC (figure 7). Baghouse filter capital and operating costs would be lowered due to the reduced byproduct solids load. A prescrubber serves to quench the gas to scrubbing temperatures of between 120° F and 140°F, remove particulate matter and saturate the gas stream. The gas is then passed into the absorption section where it is contacted with the absorbent. SO2 outlet concentrations are typically between 100 and 150 ppm, but the units can be designed for outlet concentrations as low as 10 ppm.
The gas is then reheated and sent to a traditional stack or, without reheat to a wet stack.
The aqueous amine absorbent is regenerated by conventional steam stripping and recycled to the absorber. Cansolv System FGD units can be operated at high turndown ratios. Start-up is simple and rapid. Absorbent circulation rates can be quickly changed to match changes in SO2 inlet concentrations.
Emissions. The Cansolv System FGD process in conjunction with an FBC produces little waste (Figure 8). The only solid wastes would the ash recovered from the boiler. This ash having no calcium would be relatively neutral in pH. In addition, the quantity of ash generated would not be a function of the sulfur content of the fuel. Unlike with conventional limestone scrubbing, there would be no disincentive to burning the highest sulfur, lowest cost fuels possible. The economic advantages of burning high sulfur fuels could now be fully realized.
Because the process can reduce SO2- flue gas concentrations to 10 ppmv or lower, the process will never be out of compliance with even the most stringent regulations that may be imposed in the future. Existing Cansolv System FGD units could easily and inexpensively be retrofitted to meet the most stringent requirements.
The capital cost of the Cansolv System FGD process is competitive with conventional wet limestone scrubbing, while the operating costs are significantly lower, especially for higher sulfur fuels.
Tons (dry) per ton of coke feed
NOx emissions levels from FBC are in general lower than from pulverized coal boilers, so uncontrolled NOx emission levels from FBC may meet the applicable requirements. If lower levels of NOx are required, SNCR can be utilized. This is a relatively low cost control method giving NOx reductions of 60% to 70%.
The degree of NOx emission reductions with SNCR is typically limited by ammonia slip, which manifests itself as a plume. The first unit operation of the Cansolv System FGD process, the prescrubber water spray which serves to quench the gas, remove particulates and strong acid such as sulfuric, nitric and hydrochloric. The acidic nature of the prescrubber spray ensures that any residual ammonia (slip) is collected. Ammonia slip thus being controlled, the SNCR ammonia additions can be increased to achieve a higher level of NOx reduction.
Byproducts. The process produces a pure, water saturated SO2 stream (97% SO2, balance water), that may be utilized on site as such, converted to sulfuric acid or sulfur, or shipped offsite using the SO2SAFE Storage Technology. There are numerous industrial uses for SO2, currently supplied as liquid SO2 or produced on site by burning sulfur.
SO2SAFE SO2 consists of shipping the SO2 dissolved in the absorbent and regenerating the absorbent at the user's site on demand. In this manner, the costs of handling and storage and the hazards associated with liquid SO2 are avoided. Transportation within a radius of up to 300 miles would be economical.
The water saturated pure SO2 byproduct is utilized extensively in the pulp and paper and corn wet milling industries. It can also be used to produce certain chemicals such as sodium sulfite, bisulfite and hydrosulfite. Liquid SO2 which is utilized in these applications is priced at $275/ton CAD, fob Copper Cliff, ON. If desired, the sulfur dioxide can be converted to sulfur or sulfuric acid by conventional technology.
In the continental U.S. there are about 100 sulfuric acid plants. Sulfuric acid is utilized in a large number of industrial processes. The largest consumer is the phosphate fertilizer industry, which is concentrated in Florida. Areas such as these where the value and demand for sulfuric acid is highest, would provide attractive returns on the byproduct.
Every petroleum refinery has a Claus sulfur unit on site. It is relatively simple to feed the SO2 directly into the Claus unit for conversion to elemental sulfur. The addition of pure SO2 to the Claus unit feed would result in an increase in the sulfur production capacity of the unit. Refineries also are the source of petroleum coke. Ideally a refinery supplying petroleum coke to a nearby FBC operator would accept the by-product SO2 and convert it to elemental sulfur.
Sulfite Pulp Mills(Back to Top)
Deficiencies of this mill flowsheet include significant SO2 and/or ammonia emissions, chemical imbalance in the mill and the expense of SO2 makeup, all of which complicate mill operation and raise operating and capital costs. SO2 recovery and recycle with the Cansolv System SO2 scrubbing process, rather than with ammonia, reduces emissions, makeup requirements and total cost. Recovery and recycle of the SO2 as a pure gas, rather than as ammonium bisulfite, is a further major Cansolv advantage: the chemical imbalance is eliminated and the cooking liquor preparation and SO2 recovery operations are decoupled. This decoupling removes severe operating constraints from the mill operation. Full application of Cansolv System SO2 scrubbing has the potential to yield a major increase in mill operating margin, while improving environmental performance and safety.
Deficiencies of conventional flowsheet. Ammonia-based sulfite pulping as currently practiced has a number of deficiencies which detract from the economics, environmental impact and operability of the process. Reduction in the impact of these factors could enhance the competitiveness of sulfite pulping, which otherwise is a very desirable process. The deficiencies of the conventional process are discussed below.
Chemical imbalance. The most serious drawback to the conventional sulfite mill flowsheet is the fact that while the cooking liquor consumes both combined and free SO2, the recovery operations yield mainly combined SO2. This inevitably leads to chemical imbalance: the quantity of combined sulfur dioxide recovered is greater that required in cooking liquor preparation. By mass balance, the excess must be either emitted to air or water, or transferred off site. This loss must then be balanced by fresh SO2 makeup from the sulfur burner or purchased SO2 . The operating, maintenance and raw material cost of a sulfur burner is a considerable cost penalty resulting from this deficiency. In addition, many mills supplement their SO2 requirements with purchased liquid SO2 to adjust free SO2 to levels not attainable with the sulfur burner.
The difficulties of coping with the chemical imbalance constraint are exacerbated by the fact that operation of the recovery boiler is coupled to that of the acid plant (cooking liquor preparation area). Unscheduled recovery boiler outages, the production of pulp grades requiring high free SO2, changes from a high total SO2 grade to one requiring less combined SO2 all cause changes in the inventory of SSL and weak acid (ammonium bisulfite) and create scheduling and inventory management difficulties, adding to plant operating complexity.
Feed chemical usage. The recovery of sulfur fed to the digesters is typically about 80%. About 2% of the sulfur leaves with the washed pulp and essentially all of the rest is due to the inefficiency of the recovery system. While some of the losses will be difficult to control, being in the form of dilute equipment wash waters for example, a significant reduction in losses is possible by application of better technology.
The ammonia is not recycled at all, since it is burned in the recovery boiler. However, excess ammonia consumption can be caused by air oxidation of sulfite to sulfate in the recovery process. Since ammonium sulfate is not active in the pulping process, the contained ammonia is wasted.
If caustic is used for the final cleanup of gas streams prior to venting to atmosphere, it is lost to waste water on a once through basis, as is the captured SO2.
Energy consumption. The use of multiple stages of absorption in the SO2 scrubbing system leads to an unnecessarily high gas side pressure drop, requiring powerful fans. If candle filters are used on the recovery boiler to control ammonium bisulfite aerosol emissions, these add to the pressure drop in the flue gas cleaning system. Also, in cases where the cooling water temperature is high, chillers may be required to cool the gas stream in order to get acceptable SO2 removal.
Capital cost. The complexity of the SO2 recovery system, with multiple absorbers, storage tanks, pumps, candle filters, chillers etc. leads to a high capital and maintenance costs and large space requirements for the SO2 recovery system.
Environmental compliance. Meeting stringent emission levels with ammonia scrubbing requires operating the recovery system at the limit of its capabilities. With ammonia scrubbing, a delicate compromise has to be struck between high SO2 removal and low ammonia or ammonium bisulfite emissions: it is very difficult to obtain both simultaneously. This is the justification for final polishing of some streams with caustic prior to venting to atmosphere. The waste water treatment system disposes of the sodium sulfite after treating to adjust chemical oxygen demand. If candle filters are used, the water washes required to remove the captured ammonium bisulfite can contribute to ammonia discharged to receiving streams.
If all the lignosulfonate cannot be burned in the recovery boiler due to chemical imbalance, disposal of the material can be problematic. While there are established uses for lignosulfonate as a cement additive for example, the market is not very large. Use of lignosulfonate as a road dust suppressant is possible, but it has raised questions of environmental impact.
Fugitive emissions from various sources such as pulp washers, sulfur burner etc. can also impact on the emissions and particularly the level of ambient SO2 within the plant itself.
Cansolv in sulfite pulping. All of the deficiencies of current sulfite pulping technology can be reduced or eliminated by the use of Cansolv System SO2 recovery and recycle instead of ammonia or magnesium hydroxide scrubbing. The most important benefits result from the recovery of the sulfur as pure sulfur dioxide:
Removal of these two constraints simplifies plant operation, reduces equipment complexity, allows maximum use of free SO2 where this improves quality or reduces cooking time and allows total burning of SSL in the recovery boiler. The very high recovery efficiency of the Cansolv System SO2 scrubbing process maximizes sulfur recovery and minimizes emissions, both to air and water.
The Cansolv Absorbent DS actually inhibits oxidation of SO2 to SO3, the amount of sulfur dioxide is increased due to reduced losses to sulfate. Also, since the absorbent is totally non-volatile, no amine bisulfite is emitted, avoiding the use of candle filters. Since the absorption of SO2 can be performed in a single vessel, equipment complexity, fan power, space and maintenance can all be reduced compared to current technology.
Beyond the obvious application of Cansolv System technology to simply replace the conventional SO2 absorption system with a more efficient and less costly technology, new possibilities for further simplification and cost reduction become possible. Firstly, if the mill operates a fossil fuel fired boiler, replacement of low sulfur emission compliant fuel by a cheaper high sulfur product such as petroleum coke, liquid fuel or coal becomes an option.
The payback for the investment in Cansolv System flue gas desulfurization is usually less than 2 years, particularly if a common regenerator is used for the absorbers on all the different gas streams. The sulfur dioxide recovered from the high sulfur fuel can be used to reduce the sulfur burner duty, reducing sulfur purchase requirements. In effect, the sulfur content in high sulfur fuel has a negative cost. Considering the reduced sulfur makeup requirement resulting from the higher recovery efficiency of Cansolv scrubbing, the extra sulfur input from the high sulfur fuel may be sufficient to shut down the sulfur burner. If required, elemental sulfur added to the boiler or the recovery boiler could make up any shortfall. Elimination of the sulfur burner (or purchased SO2) is a desirable cost reduction and operating simplification step.
The application of Cansolv System technology to a sulfite mill is shown in Figure 9.
The next installment of this article will discuss the application of Cansolv for SO2 transport and handling, as well as results of pilot demonstrations.
Edited by Alan S. Brown
Sulfide ore smelters offer potential uses for Cansolv System SO2 scrubbing in addition to the acid plant applications discussed above. Weak primary metallurgical gas and fugitive emission streams, from sources such as converters and driers, are costly to control by feeding them into the acid plant. Acid plant investment and operating costs are largely determined by gas flow. The large quantity of inerts in weak SO2 streams necessitates a large additional capital investment for little increase in acid production, while increasing total SO2 emissions to the atmosphere.
In natural gas, growing demand and rising prices are making the production of sour gas economical, leading to a growth in sweetening and sulfur recovery capacity, while having to deal with the tightening of emission regulations.
(7%S, 0.5% ash. 95% sulfur removal)
Ammonia based sulfite pulp mills utilize ammonium bisulfite plus dissolved sulfur dioxide as the chemical reagent to delignify wood in order to produce a cellulose pulp. Unreacted SO2 from the cook is recovered by scrubbing the blowpit gases with aqueous ammonia. The sulfur and energy contents of the lignosulfonate present in the spent sulfite liquor (SSL) are recovered by burning the SSL in a recovery boiler. The flue gas is also scrubbed with aqueous ammonia to recover the SO2. Makeup SO2 is provided by a sulfur burner and/or liquid SO2.
Managing Editor, Chemical Online