Testing is Required to Select Seal Materials for Blister-Prone Applications
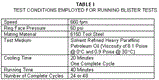
Rather than simply selecting materials based on their composition, functional performance testing is required to select seal materials for blister-prone applications. This was the most important result when 24 commercially available seal carbons, representing many different combinations of base materials and impregnants, were tested under identical conditions in an attempt to determine how material type affects carbon blistering. The fact that seal materials can not simply be selected based on their composition is highlighted by the performance of antimony-impregnated carbons, which are commonly thought to be blister-resistant. While the two best performing grades in the study were antimony-impregnated, six other grades with the same impregnant gave widely varying results, ranging all the way down to near the bottom.
Blistering is a common problem in any seal application that involves oily process fluids and thermal cycling. Shiny spots form on the face of the seal that eventually start to lift off the face and finally destroy the seal surface. There are several competing theories on why blistering occurs. One is that oil gets trapped in subsurface porosity of the seal and expands and causes the carbon to break out. Another theory is that shear torque at start-up is responsible. Everyone agrees that the result is a high spot that separates the seal from the counterface and causes the failure. This problem can be seen in gearboxes and auxiliary power units in aerospace applications, compressors on automotive air conditioners and other similar applications.
Since there is probably no single mechanism that causes blistering, it's not surprising that there are no generally agreed upon cures. Engineers at Morgan AM&T recently performed an investigation of the performance of various seal materials in a test rig designed to simulate conditions that would tend to promote blistering. All testing was done in a drill-press-mounted test rig that allowed for the temperature cycling of the oil by generation of frictional heat. A blister-test damage index was established for rating the performance of the seal grades tested under this investigation. The index involved the estimation of the percentage of wear face damage occurring during blister testing which was determined by comparison to a set of blister test standards established by using an image-analyzing computer. Testing was done under conditions severe enough to cause microcracking and pitting of the carbon seal wear faces.
The standards for the blister test damage index were established by testing different carbon seal materials of known "good" and "bad" blister resistance. Following testing on the drill press mounted rig, the external surfaces of the tested seals were painted white, after which their wear faces were carefully wiped clean with acetone soaked "Q-Tip" swabs so as to remove the excess white paint. The painting and cleaning procedure was used to highlight the microcracks and pitted (blistered) areas on the wear faces of the tested rings. After completing the preparation process, each seal was photographed by a video camera that projected an image of the entire seal face on a monitor screen. The image was projected by a half-million pixels, each measuring 0.00328 mm2. An image analyzing computer connected to the monitor screen physically measured the non-damaged portion of each wear face by counting the number of pixels contained in the remaining black area and multiplying by 0.00328 mm2 per pixel. A percentage value for the damaged area subsequently was obtained by employing the measured black area remaining after testing and the original wear face area.
A very simple, low cost, and extremely useful procedure for rating carbon blister resistance was established by employing as standards the rings actually examined earlier by using the image analyzing computer. Under the simplified procedure, the tested seals were still prepared for examination by painting them white followed by the cleaning of their wear faces by wiping with acetone soaked "Q-Tip" swabs. The wear faces of the tested seals were then visually compared against those for the standards which had been grouped into five (5) different levels of damage. The five levels of damage were arbitrarily identified as Level "0" to "4" with 0 being the best (no damage) and 4 being the worst (most damage).
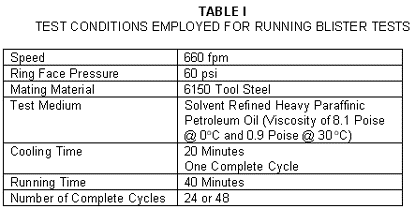
The standard blister test procedure followed under this test program called for two seals of each grade to be tested for 24 cycles at the conditions listed in Table I, followed by the testing of two additional seals of each grade at the same conditions for 48 complete cycles. After each seal was tested and prepared for examination by painting, its wear face was visually compared against those of the standards and it was assigned a "Level of Damage" which later was employed in the calculation of the material's overall "Damage Index." This procedure was accomplished as follows:
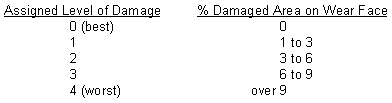
The overall "Damage Index" for a given seal material was then obtained by employing the following formula.

Table II presents the "Damage Indices" calculated for the seals of 24 different grades when tested per the conditions outlined in Table I. The ranking of the grades in Table II is from the best (at the top) to the worst (at the bottom). A review of the impregnants contained in the 24 seal ring grades shows no real correlation to exist between the type of impregnant used and where the resulting grade falls in the relative ranking. For example, antimony is commonly considered to be one of the best impregnants as far as blister resistance is concerned, and was indeed the impregnant contained in the two grades found under this study to be most blister resistant. However, antimony was also contained in other grades dispersed throughout the entire ranking of seal materials. Likewise, intuition suggests "all carbon" grades (carbonized resin) should be more blister resistant than resin impregnated grades, but the results of this study have revealed that that assumption is not necessarily true.
RANKING OF SEAL GRADES BY BLISTER TEST DAMAGE INDEX
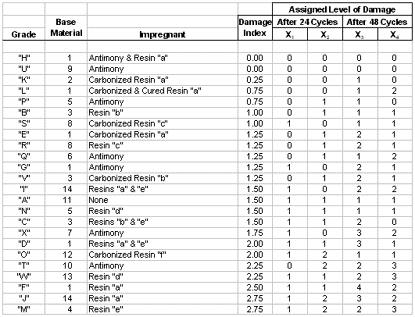
Note: Test Conditions: Run in paraffinic oil at 60 psi face pressure against tool steel for 24 or 48 cycles. Each cycle consists of 20 minutes cooling and 40 minutes running.
Damage Index = ((X1 + X2)×2 + (X3 + X4))/n; Where 0 is best and "n" is number of blister tests run.
Since the ranking of the grades in Table II relative to blister resistance is disappointing in that it does not show a specific type of impregnant to always be the best, one might question if the relative ranking of the grades is indeed real. In other words, would the relative ranking change if different test conditions were employed? (A similar study reported by E. W. Strugala in "Lubrication Engineering" showed that blister resistance is improved by switching from tool steel to silicon carbide as the counterface material, and also is greatly affected by the viscosity of the oil employed during testing.) In order to answer this question, a cursory investigation was conducted during which antimony impregnated Grades "T" and "U" were run against silicon carbide while submerged in four different oils (Table III) representing two oil types at different viscosity. (The other test conditions were the same as those listed in Table I for the 24 cycle test.) Changing from tool steel to silicon carbide as the counterface material did improve the blister resistance of Grades "T" and "U" to the point where the extent of the damage sustained during the 24 cycle tests was not severe enough to allow for the use of the blister test damage index described previously. Instead, a very simplified rating system was devised under which a number "1" was assigned to a grade when wear face surface pitting was noted after testing, and second number "1" was assigned if any microcracking of the wear face surface was observed after testing. The grades ranked under this simplified procedure thus displayed either a "0" (best), "1," or "2" (worst). The results presented in Table IV show Grade "U" to be more blister resistant than Grade "T" which matches the relative ranking of the two materials in Table II. Hence, we know the relative ranking of the 24 carbon seal grades covered in Table II is indeed realistic.
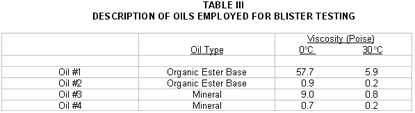
What do the results of this latest investigation into carbon blistering really mean? In themselves, the test results are rather meaningless except for the fact they demonstrate that the relative blister resistance (ranking) of carbon seal ring grades cannot be predicted, but instead must be determined by functional performance testing on a suitable test rig. Hence, anyone trying to resolve a carbon blistering problem through material substitution only must either conduct the necessary performance tests required for rating blister resistance, or must be aligned with someone who indeed is running such tests. The best combination of seal grade, counterface material, sliding speed, nose pressure, and oil type and/or viscosity to be employed for achieving the best possible blister resistance can only be determined by functional performance testing.
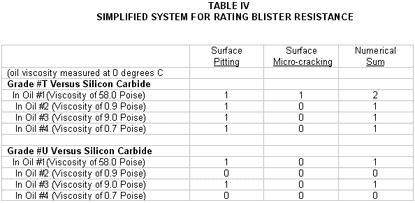
Note: For the numerical sum, 0 is the most blister resistant and 2 is the least.
About the author:
Neal Fechter is Director of Morgan Carbon Technology, a Parma, OH, division of Morgan Advanced Materials and Technology. For more information contact:
MAMAT/Americas
441 Hall Ave.
St. Marys, PA 15857
Tel: 814-781-1573
Fax: 814-781-9249