Reinforcing the Rugeley Chimney
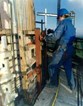
In 1997, Bierrum carried out a survey of the 180-meter high main chimney at Rugeley power station and found the top section in very poor structural condition. Bierrum engineers inspecting the site recommended strengthening the damaged section, taking into account the extended service life required by the station's owners, Eastern Generation.
The top section of the chimney had suffered from exposure to flue gases and weather for more than 30 years, resulting in a corroded and loose covering. It was necessary to restore the structural integrity of the chimney without delay. Bierrum had to produce a solution to the problem that could be implemented quickly and carried out at heights of more than 150 meters above ground.
Bierrum proposed constructing a new reinforced concrete structural cladding around the outside of the top 25 meters of the existing chimney windshield. The 200mm thick cladding is designed to relieve the existing top section of the chimney of all wind loading. The new structure provides a permanent solution and gives an extended service life of at least 20 years.
As the new cladding completely covers the old concrete surface, the need for frequent patch repairs to the top section of the old windshield was eliminated, which continues to provide Eastern Generation useful savings to the maintenance budget. And by taking the approach it did to the problem, Bierrum ensured the chimney remained in service during the repair operation.
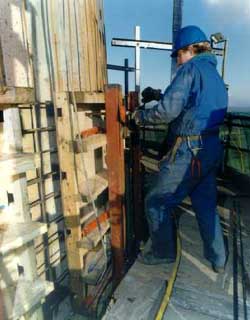
Bierrum's patented access system provides plenty of working space around the tower's full circumference at three levels.
Bierrum's patented access system has been used many times in recent years for cladding work on both chimneys and cooling towers. The system uses self-contained units, known as rigs, which climb up or down the structure. By using working platforms, the system provides safe access all around the chimney at three levels.
The Bierrum system can accommodate not only the curved shape and tapered profile of a chimney, but also the change in slope of a cooling tower. The system is used worldwide for the construction of new cooling towers and other tall structures and even for demolition work.
Initially the rigs are raised to the starting level using winches, or alternatively they can climb the structure under their own power, which means there's no requirement for large and expensive cranes. Access to the working platforms is provided by a hoist that carries both personnel and materials. This arrangement allows quick and safe access to the construction area, not only for Bierrum personnel, but also for the plant's personnel or company representatives wishing to get a first-hand look at the work being done.
The large Rugeley chimney required up to nine cubic meters of concrete for the concreting cycle. To carry this amount of concrete as well as other materials and personnel to the job site high above ground, Bierrum used a twin cage hoist. Use of the twin cage hoist allowed the concreting process to be completed in six hours, comfortably within the working day.
Each construction cycle required two days and included fixing the reinforcement, raising the shutters, lifting the rigs to the new level for the day's concreting, and finally pouring the concrete. In many applications, it's possible to complete the entire cycle in one day, and so complete a lift of concrete every working day.
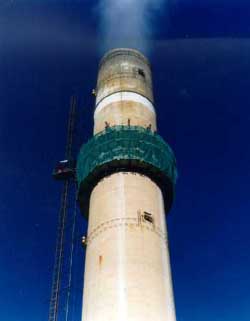
The Rugeley power plant's chimney remained operational throughout Bierrum's reinforcement project.
Careful attention has to be paid to the early strength of the concrete. The access rigs are carried on the section of the cladding that is two lifts below the current level, ensuring that the concrete strength is sufficient to carry the loads.
Typical of the attention to detail required in this type of work, temporary aircraft warning lights were fitted to the access system to replace the chimney's own lights when these were obscured during construction. The original lights were refurbished and finally fitted in position on the new structure.
At Rugeley, concreting was completed in 1998 and was timed so that the top lift coincided with a planned outage, which also helped with the chimney cap replacement work. The Rugeley chimney now has a new lease on life. From the initial inspection and the engineer's report to the design and successful execution of the construction works, all this is part of the Bierrum solution.
About the author: Paul Sayer is a contracts manager for Bierrum, a U.K.-based firm that provides a variety of concrete repair, maintenance and demolition services for power plant and other industrial chimneys and cooling towers. For more information about the company, the Rugeley project or other products and services offered, contact Hugh Bierrum, hugh.bierrum@bierrum.co.uk or Bob Sutton bob.sutton@bierrum.co.uk.