Plant controls sometimes need a tuneup
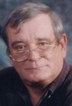
Sidebar: Q&A with John Gerry, ExperTune president and Michael Ruel, Top Control president
Electronics that eliminate the need for constant human monitoring of industrial process, including electricity generation, sometimes need a bit of tweaking and tuning up themselves. The bonus is payback in a short term.
That's where ExperTune of Hubertus, WI comes in, according to John Gerry, president.
"We optimize the loops and the system in the plant," Gerry said, "and that means optimizing tuning parameters, diagnosing when loops interact, what the causes are of the interaction, diagnosing valve problems. The software tweaks or adjusts the control system so that the plant is optimized. It can make a tremendous difference."
According to Michael Ruel, president of Top Control (www.topcontrol.com) of Quebec, "Usually, the return on investment is in weeks, not months." Plus the optimization software helps point to equipment problems that otherwise would go unnoticed, like valves that aren't properly sized or aren't operating quite right, he said.
Top Control, on the other hand, either uses ExperTune's software to optimize controller operation or trains plant employees to do the work themselves. The company normally works in North America and usually finds loops in good shape, said Ruel. After an initial tuning, a trained technician can tune six to eight loops a day.
Working relationship
Top Control has a working relationship with ExperTune, which Gerry formed in 1986 as Gerry Engineering Software and renamed ExperTune in 1995. The agreement enables ExperTune to concentrate on its business of developing software while Top Control focuses on the software's service/applications end.
To illustrate a need for optimization, Gerry made a comparison with diesel engines off the same production line that easily could be controlled by the same computer module because they are all alike and share same operating characteristics. "You optimize one, you've got them all," he said.
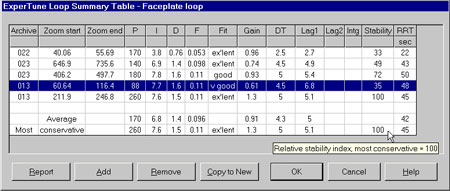
But an individual generating plant, while having similar brothers and sisters, is a unique, custom-built facility with its own individual operating characteristics and with different equipment than related plants.
Monitoring the control system
Gerry emphasized that ExperTune's software doesn't control the controller but instead monitors the control system, for example, for electronic noise that can interfere with signals or for its overall efficiency, while helping diagnose plant problems that could slice efficiency.
"Your control system is always in control of this plant," he said. "This is an off-line tool. Once we get the data from the plant, then you analyze it off line. The software tweaks or adjusts the control system so that the plant is optimized. We're not going to check the burners and make sure there's not a leak. What it does is make sure that the loops, the temperature controls of the burners, the energy output of the burner, are optimized."
But, he added, data obtained could result in changes to burner settings.
ExperTune expects to introduce a product that will constantly monitor plant control systems maybe around mid-year for testing. Sites will be selected carefully and in conjunction with Top Control.
Efficiency and nuclear plants
There is no doubt in Gerry's mind that optimized plant control contributes to efficiency, particularly in nuclear plants, where controls are sensitive to slight changes in plant dynamics and trip off line easier than conventional generation.
"If the loops are trimmed properly, there are fewer trips," he said. "They handle load changes better."
Valves can be big problems
Both Gerry and Ruel indicated that valve troubles appear to be widespread and tough to find without software guiding the way. The problems range from sticky to under- and oversized- units that sometimes cause unnecessary downtime to investigate and replace "suspected" malfunctioning units.
Said Gerry, "You may have to change valves less, do less maintenance on valves. It's an easy thing to think that the valves are OK when they're not. It's not something that any engineers think of."
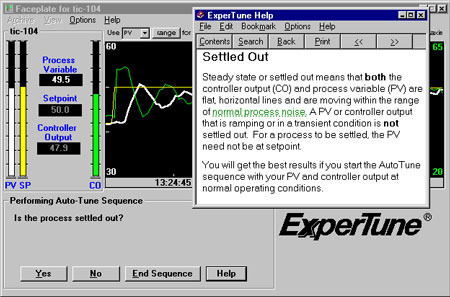
If the diagnostic points to a problem and the plant can't be taken down, ExperTune's software helps pinpoint parameters to run as best as possible until maintenance can be scheduled.
Valves can stick, said Ruel, explaining that balky valves are like trying to move a heavy piece of furniture. "If you're not strong enough, you push, you push. Then you push too much," with the furniture overshooting its intended position
A sticking valve suddenly opening creates a "bump" in the flow of whatever it's controlling, which could affect the smooth operation of loops, like a line of toppling dominoes. Overall, plant efficiency suffers.
Ruel likes the way ExperTune's "shrink-and-swell" programming handles the changes in water temperature and behavior when feedwater is added. "Other packages on the market are unable to handle such processes," he said.
Standard, advanced offerings
ExperTune's product is available in standard and advanced levels.
The standard version includes:
- PID tuning for load upsets or setpoint changes.
- Safety adjustments for trading off between robustness and response.
- Indications of performance improvements with new settings.
- Process modeling up to the second order with dead time to include integrators.
- Time simulation of setpoint changes or load upsets, including what-if analysis of current to new parameters and simulating new values without affecting plant operation.
- A robustness plot covering the tradeoff between tight tuning and sensitivity to dead time or gain changes.
- Process frequency response compared to models.
- Automatic hysteresis check and ways to improve control by reducing hysteresis.
- Graphic zoom-in for editing, filtering or averaging time data.
- Statistical analysis to reduce variability to increase produce quality and capacity.
- Support for all single-loop controllers and PLCs.
- Reports on loop analyses in MS Word.
- Connections to PLCs and single-loop controllers via setup wizards with OPC or DDE options.
- OPC communications option.
- ASCII communications option.
- Multi-channel communications option, including DDE or ExperTune's A/D converter.
Advanced version offerings
The advanced version adds:
- PID tuning table to summarize tests.
- Traditional Lambda tuning rules, including Lambda for level.
- Performance summary window.
- Time simulation to compare actual to model.
- Time simulation of simulated response to noise, including valve wear indices.
- A robustness plot to dial in preferred robustness.
- A hysteresis check to choose locations manually.
- An analysis indicating how valve life has improved.
- Support for all DCS controllers.
- Valve wear analysis.
- PV filter analysis.
- Valve stiction wizard to correct stiction problems to reduce cycling.
- Multi-variable loop analysis for adding extra loops and matching variables for modeling, analysis, simulation, tuning or interactions between loops.
- Multi-variable loop analysis for relative response time. decoupling interacting loops and cascades.
- Multi-variable loop analysis for auto and cross correlation.
- A characterizer for determining optimal performance at all production rates.
- Universal linearizer for pH loops for control with little or no cycling.
- Power spectral density for for pinpointing process faults by finding hidden cycles.
- Histogram for identifying problems from normal operating data.
- Inverse response for minimizing effects of shrink-swell.
- Customized report templates in MS Word.
- Set point filter for response to both loads and set point changes.
- Setup wizards for connection to DCS systems with OPC or DDE options.
- Manual settings for min-max on time plots.
Q&A with John Gerry, ExperTune president and Michael Ruel, Top Control president
Where is computer technology heading in the generation business?
People will more effectively use the control systems that they have by focusing on performance in these areas:
- Applying optimization tools to systematically optimizing every loop.
- Maintenance and performance monitoring.
- Control systems with more complex control strategies.
- Automated troubleshooting and data analysis to improve maintenance and increase uptime.
- Automated operation based on energy price, demand and availability.
Do you somewhere down the road see generating plants being operated with maybe a small staff or no staff on site and instead monitored from a central location?
The emphasis will be on increasing performance and reducing trips and downtime. Monitoring and supervision through the internet will also increase.
How much of a role does computer technology play now in the generation business in light of competitive generation and the bottom line?
Without computer control technology, fossil plants would simply not be competitive. Successful operations realize this and focus on getting the most out of using computer technology to make their plants as efficient as possible. The computer is not an end in itself but simply a tool to make the plant efficient.
Do you see a point where technology rather than fuel prices will be the main factor that determines whether a plant is profitable?
Absolutely. Operating decisions based on real-time economic data will increase profitability. There will be a more direct link between customer demand and market availability of fuel, offer price and actual price. The most significant impact on profitability will come from two areas, applying existing optimization tools and from a new level of automation.
Systematically going through and optimizing each loop in the plant impacts the bottom line. The new level of will be automated maintenance, automated performance analysis, automated control system performance monitoring, automated operation. All will significantly impact efficiency.
How quickly has technology advanced from its early days, a brief history please?
- Beginning of the 20th Century, control systems replace hand operation.
- About 1940, control rooms and centralized operation.
- About 1950, electronic control systems.
- About 1960, computers are used mostly for monitoring than for control.
- About 1975, distributed control systems with a network collecting data, screens began to replace large control rooms.
- 1980-90, control systems benefit from fast and powerful processors with more control functions, advanced control strategies and data acquisition.
- Recently, internet and modern operating systems bring the office and the control systems together, linking the production to the price of energy. We can link real-time data analysis with performance.
- The foreseeable future will see more links between economics, performance and operation.
About the author: Joe Palenik covers a variety of power generation topics for trade publications around the world and is regularly featured on Power Online and ElectricNet, a VerticalNet community for the transmission and distribution industry, www.electricnet.com. To contact Palenik, write writer@dmv.com.
Subscribe to our free e-mail newsletter.
Click for a free Buyer's Guide listing.