Orkot Bearings Used In Three Gorges Dam
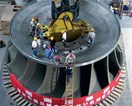
Orkot® fish-friendly bearings aid power generation in the biggest dam ever constructed
Based on independent test results Alstom adopts Orkot bearings from Trelleborg Sealing Solutions on turbines for hydropower generation. The composite technology offers significant advantages over the traditional bronze solution. In particular, the exceptional friction characteristics of Orkot means bearings give long service life and operate without lubrication. This makes them ‘fish-friendly', an important consideration when in contact with water in hydro turbines. Now a proven solution for Alstom, Orkot bearings will be fitted on a number of turbine runners in the largest hydropower project ever built, the Three Gorges dam in China.
The Three Gorges hydropower plant is China's biggest construction project since the Great Wall. A gravity type dam, it will retain the water from 4,500 kilometers (2,800 miles) of the Yangtze. Stretching 2.4 kilometers (1.5 miles), it is expected to create as much electricity as 18 nuclear power stations. Providing an estimated one-ninth of China's energy, it will replace 40 to 50 million tons of raw coal combustion each year.
Alstom Power, the world's number one in hydropower generators, will be supplying almost half of the hydro turbines and generators for the Three Gorges. Their runners are 23% larger than any others produced by them before. These are a massive 10.6 meters (35 feet) in diameter with a height of 5 meters (17 feet).
For hydro turbines on the right bank of the Three Gorges dam, Trelleborg Sealing Solutions is supplying Orkot bearings of an advanced reinforced polymer material. The bearings are fitted on wicket gate housings within the Alstom hydro turbines. These are adjusted to control water flow and bearings aid their movement.
Bronze bearings have been a traditional solution in hydropower turbines but to give them sufficient friction to work they require lubrication. During operation, the lubricant enters the water, which has a detrimental effect on wildlife. Environmental pressure means that greaseless ‘fish friendly' bearings such as Orkot must now be fitted on hydro turbines. In fact, Alstom was a leader in this practice and have fitted self-lubricating bushes for more than thirty years.
As an alternative to proven products Trelleborg Sealing Solutions offered Alstom Orkot advanced polymer bearing technology. Orkot appeared a cost effective solution but Alstom was skeptical about the product's ability to work effectively. However, Trelleborg Sealing Solutions could support its performance claims for the product with independent reports.
The tests undertaken were specific to bearings in hydropower applications. The Orkot performance was measured against bronze bearings and competitive composite solutions. In all cases Orkot outperformed the other products. Their exceptional friction characteristics mean that they have a very low co-efficient of friction in dynamic situations and especially at start of movement after extended periods of rest. In fact, the coefficient of friction is almost as good at start up as it is in the dynamic state. This was important in the Three Gorges turbines where once the optimum flow of water has been established, the bearings within the runners would be quasi-static for a considerable period of time, perhaps several hours.
The Orkot TXMM and TLMM materials used in these bearings are unique. A polymer material, the elasticity of the Orkot product is also significant in the functioning of the bearings. As opposed to a metal bearing, the Orkot material is relatively soft. When a load is applied to the material, it gives very slightly, deflecting or deforming in shape. This material property improves the life of the bearing by reducing wear. It has the further benefit of accommodating misalignment within equipment housings. No other bearing material of this type can offer as low a coefficient of friction along with the same level of elastic properties and load bearing characteristics.
Summary of test results
Dinorwig power station comparison tests
A review of alternative designs of bearings was undertaken at Dinorwig power station. This was in response to significant wear on bearings caused by difficult operating conditions. Coupled with this they needed to reduce use of grease, which increased maintenance costs and was detrimental to the environment. The tests concentrated on greaseless bearings. Two samples were supplied by a number of manufacturers, including Orkot, and fitted to a single hydropower unit which was monitored for a period of two years.
Service conditions:
- Guide vane shaft material to BS 1630 Grade B stainless steel, 200 HB hardness
- Journal size 207 mm (8 inches)
- Bearing 207 mm (8 inches) ID, 235 mm (9.25 inches) OD, length 100 mm (4 inches)
- Housing material mild steel 25mm (1 inch) thick
- Load 20N/mm2 max
- Temperature 10 to 15°C (50 to 59°F)
- Shaft speed 0.625 rpm
- Arc of rotation 30°
After 12 months in service, the bearings were removed. Of the nine different bearing types, Orkot showed the second lowest amount of wear at only .04 mm over the period. After two years this ranking was retained with wear on one Orkot sample 0.055 mm and the other even less at 0.0425 mm.
Some key conclusions from the report:
- Wear of Orkot bearings was much lower than lubricated bronze bearings and all but one of the competitive greaseless bearings
- Life expectancy based on the 12 month results was around four times longer than greased lubricated bronze
- Greaseless bearing performance is more predictable than that of greased lubricated bronze bearings as these are dependent on the consistency and effectiveness of their lubrication
- Non-metallic bearings allow for some shaft misalignment
Independent report conducted by Swedish University Technology Division
In this study, four commercially available bearing materials were tested in water-lubricated conditions with an oscillating stainless steel shaft that had a motion pattern similar to a bearing supporting a turbine blade. Results were compared to a lubricated tin-bronze bearing under the same test conditions.
Test conditions:
- Shaft diameter 40 mm (1.6 inches) made of stainless steel SS 2324-02 turned to surface finish Ra 0.4 with hardness 325 HV
- Bearing length 30 mm (1.2 inches)
- Each bearing underwent 330,000 shaft motions at a maximum sliding speed of 5.6 mm/s (0.2 inch/sec)
- Friction, displacement between journal bearing halves (linear wear) and temperature were recorded
Some key conclusions from the report:
- Orkot bearings had a similar coefficient of friction at start up as a lubricated bronze bearing, the second lowest of those tested
- Orkot bearings had a significantly lower coefficient of friction in dynamic situations than the lubricated bronze bearing and much lower than all other greaseless bearings
- The Orkot bearings wear performance was significantly better than all greaseless bearings including the bronze lubricated bearing, showing virtually no wear
SOURCE: Trelleborg Sealing Solutions