New ceramic coating improves gas turbine performance
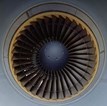
Gas turbines have long been a mainstay in power generation and the current California energy crisis only serves to underscore the need to achieve maximum performance from electricity-generating gas turbines while reducing costly and disruptive downtime. However, gas turbine performance actually suffers when operators increase firing temperatures in efforts to boost power and efficiency. The corrosive effects of hot combustion gases increase with higher firing temperatures, resulting in more rapid component wear and, ultimately, failure. In fact, traditional oxidation-resistant coatings on turbine blades are wearing out at unacceptably high rates, resulting in excessive downtime and repair costs for turbine operators - costs that can run into the millions of dollars for a set of air-cooled, nickel-base superalloy blades.
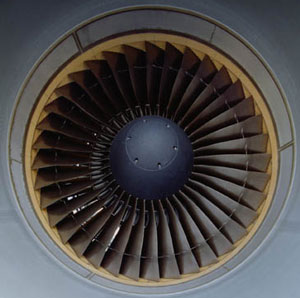
Our featured technology is a new, multi-layer, nanostructured ceramic coating designed to create a protective barrier against heat, oxidation, and corrosion on turbine blades. Protective coatings are not new - ceramic thermal barriers have been in use for years, usually applied by electron-beam evaporation or plasma spraying. But their record is spotty at best, and these coatings have only provided a marginal extension to the life of a turbine blade. However, this new ceramic coating, developed by EPRI of Palo Alto, California, introduces a novel laminated coating system which provides a number of benefits and is applied in layers measured in nanometers.
The multi-layer coating is applied by either electron-beam physical vapor deposition process or sputter coating at temperatures above 1020C. The first layer, or zone, is an oxidation barrier to protect against the damaging effects of hot gases; a second layer scatters phonons to reduce thermal conductivity; and a third layer provides optical reflectance to redirect radiant energy and can selectively reflect the specific operating temperature and thermal energy spectrum of a particular gas turbine component, such as a blade, transition piece, or combustor liner. Each major zone is actually a combination of several layers, with the total coating a mere 50 to 250 microns thick - somewhat thinner that conventional barrier coatings. Herein lies another advantage - the coating's thinness reduces stress and weight and improves the blade's aerodynamic efficiency. The laminated ceramic coating also improves turbine performance by insulating the cooling channels cast into turbine blades and vanes, reducing requirements for cooling air and the corresponding performance penalty. Further development is necessary to ready this technology for commercialization.
Subscribe to our free e-mail newsletter.
Click for a free Buyer's Guide listing.