High Performance Transformer Oil Pumps: Worth The Investment
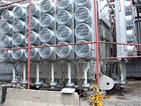
By Greg Stem, Engineering Services & Rep. Channel Manager, Cardinal Pumps and Exchangers
Transformer oil pumps have evolved dramatically over the past several decades. Once considered to be merely a replaceable routine maintenance item, comparable to say, a valve, pumps are now almost universally recognized as a critical component of "forced oil cooled" transformers a component that requires sophisticated engineering, high quality construction and systematic preventative maintenance.
When a transformer oil pump performs properly, it ensures maximum cooling to maintain the transformer's peak load capacity. However, impairments to a pump can result in costly breakdowns and potentially catastrophic damage to the transformer. Unfortunately, such impairments are notoriously difficult to detect and prevent in pumps that are designed and/or constructed inadequately.
Transformer oil pump manufacturers in the United States have provided worldwide leadership in addressing these problems by introducing design improvements and innovations such as ultrasonic sensors that monitor the condition of bearings. Major North American utility companies have also driven the development of high performance transformer oil pumps by requiring thermal, mechanical, sealing, electrical and fluid systems that provide dependable operation.
The Challenge
Pumping transformer oil is a demanding application. The pump must operate continuously, year after year, pumping high temperature oil and remain hermetically sealed, in harsh outdoor environments.
One of the most challenging aspects of transformer oil pump design is the fact that the transformer oil also functions as the pump's lubricant. The problem is that transformer oil is selected not for its lubricating performance but rather for its ability to function as an insulator to suppress corona and arcing within the transformer and for its ability to maintain stability and good dielectric properties at high temperature. Highly-refined mineral oil works well inside the transformer, but it is a poor lubricant for the ball bearing systems in many types of transformer oil pumps.
The Risk
Wear of the bearing system and impeller can lead to the release of metal particles into the oil circulating through the pump, cooler and ultimately, the transformer. As a result, the dielectric properties of the oil and insulation can degrade, potentially causing hazardous arcing.
Degradation of the bearing system and impellers, as well as impairments of motor windings, can also cause a reduction in pump flow and discharge pressure which causes reduced cooling capacity
Leaking electrical connectors and gasketed surfaces can impair pump performance and allow the ingress of moisture into the oil, as well as oil leaks into the environment.
State-of-the-art pumps mitigate these risks in a number of ways, including improvements to bearing design, ultrasonic monitoring of bearing condition, and high quality construction. Properly designed new or remanufactured pumps can take advantage of many of these advancements in transformer oil pump technology.
Bearing Design
Of all the design improvements in transformer oil pumps over the past several decades, the single most important one is the replacement of ball bearing systems with bronze sleeve bearings.
As mentioned above, transformer oil provides a poor lubricant for ball bearings. In fact, ball bearings are a viable solution only when lubricated by heavier oil or grease. They fail prematurely when lubricated by light-weight, low-viscosity transformer oil.
Additionally, ball bearing pumps that are not operated continuously will commonly fail as a result of false brinelling of the bearings caused by transformer vibration or slight flow caused by convection. False brinelling occurs when vibration pushes the lubricant away from a region that it is intended to protect. In a situation when a mostly stationary bearing is subjected only to oscillating or vibrating load, the lubricant may be pushed out of the loaded area. However, since the bearing is rolling only small distances, there is no action or movement that replaces the displaced lubricant. The resulting wear debris oxidizes to form an abrasive compound which further accelerates wear.
All U.S. manufacturers, and some foreign suppliers, have discontinued using ball bearings in transformer pump designs. North America's largest manufacturer and remanufacturer of transformer oil pumps, Cardinal Pumps and Exchangers in Salem, OH, a division of Unifin Int'l., retrofits all ball bearing pumps with pump-specific bronze sleeve type radial / thrust bearings and hardened steel thrust collars.
The key to the design of thrust and radial bearings for transformer oil applications is a large thrust face sleeve bearings for long life and minimum wear. The bearings need to have proper surface finish, and precisely positioned grooves to pass the oil and maintain an adequate lubricant film under all conditions.
Monitoring Bearing Wear
Reliable long-term performance of transformer oil pumps depends not only on the bearing and hydraulic design systems but also on the ability to pro-actively detect wear, to ensure effective and energy-efficient cooling performance and to protect the pump and transformer from damage and breakdowns.
A patented ultrasonic bearing wear monitoring system was developed in 1984 by J.W. Harley / TecSonics Inc. (a recent acquisition of Cardinal Pumps and Exchangers, Inc.) to overcome the shortcomings of conventional transformer pump bearing wear detection methods based on sound, vibration, and oil contamination. Such methods proved inconsistent and unreliable, and they were useful only after the pump was in an abnormal operating state or on the verge of catastrophic failure.
The ultrasonic bearing wear system, TecSonics™, provides advance warning. By tracking data over time, the monitoring system provides rate-of-wear information that enable informed decisions about selective, preventive maintenance, to protect equipment, avoid breakdowns, and optimize maintenance effort and expense.
The principle of operation of the ultrasonic monitoring system is not complicated. Six precision ultrasonic sensors are mounted in both thrust and radial bearings at strategic points, on new pumps or on remanufactured pumps from various manufacturers. A permanently mounted piezoelectric transducer emits a high-frequency sound wave, and precisely measures the echo time to determine the distance between the sensor and the bearing surface, to an accuracy of 0.0002 inches. Measurements are compared to baseline readings to determine if any bearing wear has occurred.
The temperature-compensated readings can be taken while the pump is under any operating condition, without disassembling the pump, whether the pump is operating or not. The sensors do not affect the performance of the pump.
In addition to the ultrasonic system for monitoring bearing wear, it is also useful to have a shaft rotation sight plug to facilitate checking for proper shaft / impeller rotation.
Quality Construction
A third consideration, beyond the design and monitoring of the bearing system, is the overall quality of construction, both in terms of the quality of materials and the quality of manufacturing.
Pumps should be constructed of rugged cast iron material for the pump castings (casings, motor enclosures, and impellers) to provide long life in the field. To protect the exterior surfaces from corrosion, high performance / high quality coatings (primer and top coats) should be applied.
All sleeve bearing pumps should have the bearing journals and thrust surfaces ground between centers to ensure alignment and surface finish. All pump shaft, impeller and motor assemblies should be dynamically balanced to assure long-term vibration-free operation.
Durable electric supply power cords also help to ensure reliable transformer pump performance. They should be capable of withstanding ultraviolet rays, oil, water and extreme weather conditions.
The Economics of Transformer Oil Pump Investment
Investment in high quality new and remanufactured transformer oil pumps has a high economic return. A good pump will typically cost much less than one percent of the cost of the transformer that it supports, and yet it provides long-term insurance against breakdown, damage or failure of the transformer. And as all owners of large critical transformers will attest, a failure or major outage of this equipment can cause severe upheaval to the wellbeing of their electrical power distribution system.
High quality pumps also pay for themselves in lowered maintenance and replacement costs. Properly designed sleeve bearing pumps reliably perform 15+ years more than 3-4 times the typical useful life of ball bearing pumps. In addition, pumps with ultrasonic monitoring systems are less costly to operate because preventative maintenance can be efficiently planned.
For more information on high-performance transfer pumps, please visit www.cardinalpumps.com
SOURCE: Cardinal Pumps