COEN Releases Ultra Low NOx Burner with Widened Stability Limits
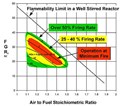
By Vladimir Lifshits and Scott A. Drennan, COEN
Ongoing NOx emission regulations present owners of industrial steam generators with a multitude of challenges in meeting increasingly lower NOx emission standards. The current Lowest Achievable Emissions Requirement (LAER) requires NOx emissions for boilers to be less than 9 ppm (at 3% O2), with future regulations expected at less than 5 ppm.
Meeting these single digit NOx emissions requirements poses important technical, financial and operational challenges to owners of steam generating equipment. Ultra low NOx burner technology offers significant cost savings over the use of post combustion treatment systems such as selective catalytic reduction (SCR). However, ultra low NOx combustion requires operation near the limits of flammability requiring ingenious burner designs to provide safe, reliable, and stable burner operation.
Novel Burner Design Uses Premix Combustion Principles to Achieve Single-Digit NOx Levels
Now, a new burner developed by COEN Company specifically addresses the challenges of ultra low NOx combustion, and provides unique reliability over a wider range of parameters.
With additional funding from the Gas Research Institute, Southern California Gas and the California Resources Board, COEN developed the QLA burner over a period of three years. COEN found during the development that meeting the NOx target was relatively straightforward with simulated premix combustion and flue gas recirculation (FGR). The real developmental challenge lay in producing a burner design that did not require an unreasonably precise control system and improved turn down (e.g., high fire to low fire ratio).
Objectives of the program were to achieve less than 5 ppm NOx emissions (at 3% O2, dry) for ambient combustion air and less than 9 ppm NOx emissions (at 3% O2, dry) for up to 600°F preheated air.
The burner must also meet less than 30 ppm CO emissions (at 3% O2, dry) and ultra low hydrocarbon emissions. Besides meeting those performance targets, the resulting burner must have several key features allowing it to be a commercially viable design, including a satisfactory turndown over a minimum of 8 to 1 and oil firing capabilities. The burner could not degrade safety or reliability for the industrial user and had to be suitable for retrofitting existing boilers.
Within the outlined objectives, the main thrust of the development program focused on improving the stability of the burner and developing a specific combustion control scheme for operation at ultra low NOx levels.
The Problem: Flame Stability at Ultra Low NOx Levels
Reducing thermal NOx production means reducing the peak flame temperature that can be achieved by premixing the fuel and air and using FGR as a diluent. As the flame temperature reduces to the levels required to meet ultra low NOx emissions, the limit of flammability is approached and the flame becomes unstable.
Figure 1 illustrates the performance of a typical simulated premix burner at various NOx levels and firing rates without air preheat. Each of the shaded areas represent regions where the flame is stable and the numbered curves represent "iso-NOx" lines.
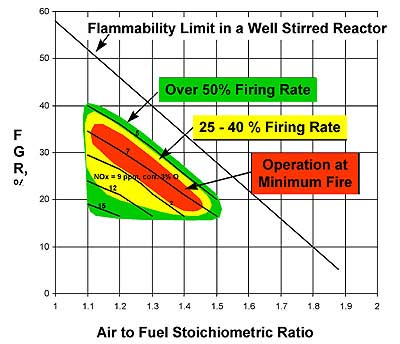
Figure 1: Generic Simulated Premix Burner Performance
This performance curve shows that there is very little margin for error at the target NOx emissions of 5 ppm. A burner with this limited margin of stability would develop flame stability problems leading to pulsation and blow out during load shifts and with changes in atmospheric conditions. This limited margin of stability puts unacceptably precise requirements on the combustion control system. The burner's stability needs improvement.
The Solution: Novel Burner Design with Multiple Fuel Zones
The QLA design solves this stability dilemma by incorporating numerous features that make operation reliable over a wider range of parameters. First, it uses three separate fuel zones to provide improved flexibility and controllability of the burner.
Second, extended turn down over 10:1 can be achieved with optional variable burner geometry. While the major mechanism of NOx reduction is simulated premix-type combustion with FGR, the burner also uses some degree of fuel staging. The positive effects of the QLA burner's design are shown in Figure 2, where the ranges of stable operation have been extended at all firing rates, especially at minimum fire.
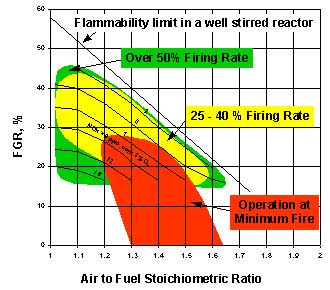
Figure 2: COEN QLA Burner Performance
These improvements in the burner's stability allow the use of simpler and more reliable controls and provide stable operation during load swings.
Demonstration Test Site
A 60,000 lb/hr balanced draft boiler at the Central Heating Plant in Sacramento, CA shown in Figure 3 became the first site for the new QLA burner. The boiler, operating year round, supplies heating and cooling to the State Capitol and 22 other state buildings in Sacramento. The boiler is equipped with two burners firing natural gas or light oil.
The Sacramento Central Heating Plant's existing burner system exhibited capacity limitations, low efficiency, low reliability and operational difficulty meeting the 30 ppm NOx emissions permit level. The plant wanted to overcome these operational and economic shortcomings and re-permitted at 9 ppm voluntarily to gain credits for a future boiler installation.
The scope of the retrofit included the burners, controls, combustion air and induced draft fans and fuel trains. The new retrofitted system had to comply with the new permit levels of 9 ppm NOx on natural gas 30 ppm CO and be able to fire gas or oil producing up to 60,000 lb/hr of steam. It also had to be tested with the air heater bypassed to demonstrate the program target NOx of 5 ppm without air preheat. The plant also required the new burner to achieve an 8:1 turn-down, fire dual fuels, and not sacrifice safety or reliability.
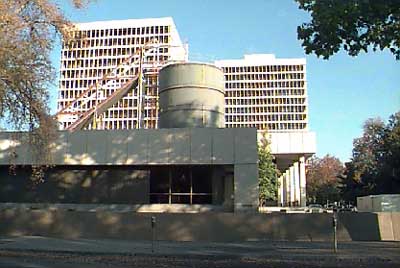
Figure 3: Sacramento Central Heating Plant
COEN supplied the new Ultra Low NOx QLA burner as a retrofit package with COEN's proprietary Fyr Monitor Control System. New fans and duct work were installed to accommodate the increased levels of FGR required to meet the NOx targets. COEN modified the existing flame safeguard system and installed new UV/IR scanners on each burner.
Demonstration Site Results
The overall performance of the QLA burner with respect to the width of the stability ranges was similar to what is shown by Figure 2. Because of massive amounts of refractory in the furnace, the actual quantities of FGR or excess air for the comparable NOx were higher by 4% to 6% than in the prototype testing. This difference can be attributed to the large area of the furnace wall covered with refractory and some leakage of air into the furnace.
Figure 4 and Figure 5 illustrate the burner NOx performance over the load range with and without air preheat. The NOx emissions data were recorded at the stack and at the back wall of the furnace. By the time combustion products reached the back wall, combustion was complete as CO emissions were negligible. However, the NOx emissions were only about 50% of those measured at the stack. So the formation of NOx continued in the furnace.
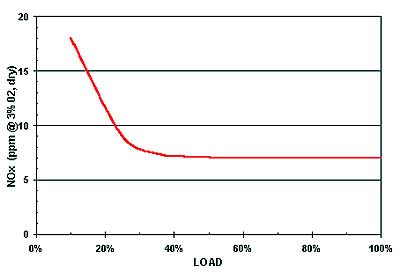
Figure 4: QLA Performance with Air Preheat: NOx vs. Load
With the increased amount of FGR and excess air, the minimum NOx emissions at the stack at high fire were measured as low as 5.2 ppm; CO emissions were well below 10 ppm. At this level, it was difficult to see the flame even in the core area. The signals from the UV scanners at this point were also weakening, so that operation, even with lower NOx, was not attempted. However, at the back wall NOx was only 2.5 ppm NOx, corresponding to 3% O2. These data indicate that the NOx emissions target of 5 ppm can be met in a modern package boiler with less refractory. During the source testing with 450°F air preheat and at full load, the unit passed easily with 7.3 ppm NOx and 3 ppm CO (corresponding to 3% O2, dry).
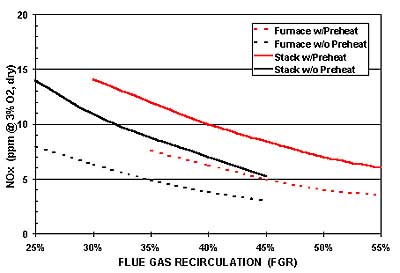
Figure 5: QLA Performance at 15% Excess Air: NOx vs. FGR
The boiler was also set to fire diesel oil with preheated air over a 4:1 turn down. When firing oil, the NOx emissions were 60 ppm with 20% FGR. The NOx emissions were lower with more FGR.
Summary and Conclusions
Different burner concepts using premix combustion can fire gaseous fuels and achieve single-digit NOx emissions with high levels of flue gas or excess air with minor differences in the relation between adiabatic flame temperature and NOx. The true comparison between these burners, or systems, should be with respect to the operational flexibility and safety over the required turndown.
The QLA burner successfully demonstrated the necessary flexibility and performance in one of the most difficult environments: multiple burner boiler; high percentage of refractory coverage in the radiant section; preheated air; fast load swings; and overall turn down of 10 to 1. The boiler was set for automatic operation with less than 9 ppm NOx over 4 to 1 turndown. The burner also showed good performance when firing diesel oil.
The threshold of flame stability is at about 2 ppm NOx. When operated with or without preheated air NOx emissions at the stack were approaching 5 ppm. Lower NOx could have been achieved in the furnace with less refractory.
Automatic operation with NOx less than 5 ppm, in this particular boiler, requires additional improvements with the controls and scanners to maintain adequate safety.
About the authors: Vladimir Lifshits and Scott A. Drennan are research and development staff engineers for COEN. Since 1912, COEN Company has specialized in the design, engineering, servicing and maintenance of burner equipment and combustion systems. For more information, call 650-697-0440, marketing@coen.com.
Edited by April C. Murelio
editor@poweronline.com