CFX-TASCflow: An important tool for Alstom Power
The importance of CFD in the turbomachinery design process has risen dramatically in the last few years, a trend driven jointly by the availability of affordable computers and powerful software.
At ALSTOM Power Technology, we have always capitalized on new developments in CFX-TASCflow, such as parallel operation or unsteady simulations, to increase the benefits to the business of CFD modeling.
This modeling covers the whole range of our products, including axial turbines for power generation in steam, gas and combined-cycle plant, as well as radial compressors and turbines in other fields.
A new design of the low-pressure part of a steam turbine with a blade height of over 1 meter led not only to new highly three-dimensional blades, but also to a new design of the flow path and labyrinths.
The overall efficiency of the thermodynamic cycle increases by drawing off some of the steam at several locations in the turbine and using it to preheat the water before it enters the boiler. However, the interaction of these bleeds with the labyrinths and the new blading can cause aerodynamic losses and must also be considered in the casing design.
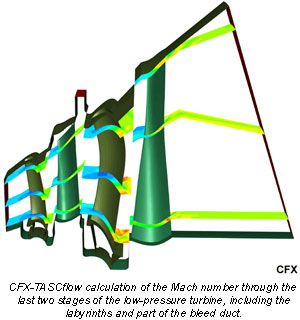
To investigate one of these bleeds—located upstream of the last stator—we considered the last two stages together with the labyrinths and a part of the bleed duct. A further complication arises since the flow in the last stages of low-pressure steam turbines is transonic and shock losses must also be minimized.
Analysis of the original geometry showed that the flow from the labyrinth entered the bleed axially at 400 m/s causing separation at the upstream wall.
Several modifications of the casing in the region of the first-rotor labyrinth and the bleed were investigated with CFX-TASCflow, leading to a new design that avoids this separation. A 75% reduction in dynamic pressure losses has been achieved, which in turn led to an increase in the overall efficiency of the thermodynamic cycle.
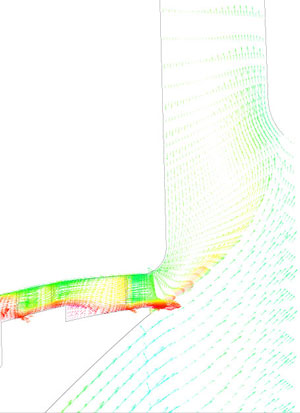
flow from the labyrinth caused separation at the
upstream wall of the bleed.
This is just one example of how we use CFX-TASCflow. The ongoing improvement of the solver, together with new CFX tools such as CFX-TurboGrid and CFX-5, allows us not only to improve our products but also to increase our understanding of the complex flows within them.
(Editor's Note: AEA Technology recently released an updated version of CFX-5, with additional solver enhancements. For more information, see AEA releases new version of CFX-5)
About the Author: Dr. Peter Leidner works for ALSTOM in Switzerland. To contact him, write Im Segelhof, 5405 Baden-Dättwil, or call 41-56-486-8281, fax 41-56-486-7359, or email peter.leidner@power.alstom.com. This article first appeared in AEA Technology's (www.aeat.com/cfx) CFX Update, 1999. It was submitted by Chris Reeves, AEA Technology, 888-827-2356, and reprinted with the approval of AEA Technology and ALSTOM Power.