Be Our Guest: Canada Plant Sees First Use of LM6000 for Synchronous Condensing
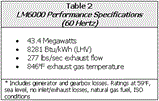
The 43-MW Poplar Hill power plant in Grande Prairie, Alberta, Canada started commercial operation under a fast track schedule on Dec. 31, 1998—just eight months after the contract signing. The plant, which is remotely operated, is powered by a GE LM6000 aeroderivative gas turbine generator-set. This project is unique because it marks the first worldwide application of the LM6000 as a synchronous condenser for grid support. This is the first LM6000 PD (Dry Low Emissions combustion system) to be placed into service by packager, S&S Energy Products, and the first such unit operating in North America.
Project History
Poplar Hill plant owner ATCO Power is an international independent power producer and the non-regulated entity of ATCO Ltd., based in Alberta, Canada. ATCO Power currently operates 1,485 MW of non-regulated generating capacity. In addition, it has almost 450 MW of projects under construction and almost 1,000 MW of projects in development (See Table 1).
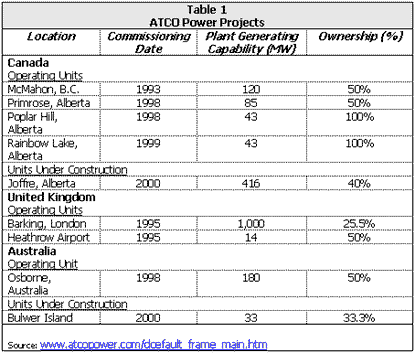
According to ATCO Power, electricity use has been growing in the province at about 3% or 150 to 200 MW per year, and can be expected to continue to grow at this rate. Shortages have been experienced during unscheduled maintenance at the provinces' coal-fired central power stations. Surplus capacity on the system has been consumed and because of the deregulation process in the province, new generation hadn't been built until these last two years. When the last major coal unit came on line in the early 1990s, the province had capacity for awhile, but this has since been used up.
In the past, utilities in Alberta would agree on the power forecast, and in turn, would submit proposals on how to build this capacity. This planning system for new generation has been replaced by a free-market approach. In response to this non-regulated market, Alberta established a power pool, where various players, such as ATCO Power, invest in new generation and can respond to electricity prices that signal the need for new supply.
In fact, ATCO Power responded to an RFP (request for proposal) from the transmission administrator and was selected to build the Poplar Hill power plant. It was designed primarily as a replacement for a proposed transmission tie project to support the transmission system in that area of the region. The power transmission system needs this added support to help keep voltage levels up and to avoid possible widespread outages of certain transmission lines and generators. A secondary result was an increase to the installed capacity in the province.
The power plant replaced the planned transmission tie project which included a new 144 kV transmission line from BC Hydro's Dawson Creek substation to ATCO's Ksituan River substation. A second 144 kV line was also required from Ksituan River to the Poplar Hill substation. The need for both lines was eliminated because the power plant offers a substantial savings to the electrical consumers in Alberta.
Synchronous Condensing
Synchronous condensers can be used to correct lower power factors, and provide a source of leading or lagging reactive current. This type of equipment is often used when quick response is needed to reactive demands. Synchronous condensers also address quality issues such as voltage regulation and flicker, and allow for finer adjustments to changes in load.
The LM6000 gas turbine-based power plant is located near a load center, and is expected to be operated 50% of the time in power generation mode and 50% in synchronous condenser service.
The LM6000 at the Poplar Hill plant operated 10 months solely in power generation mode. Then in September 1999, S&S Energy Products began the retrofit of the LM6000 by installing a clutch, manufactured by SSS Clutch Co. Ltd., New Castle, DE.
The Clutch
The clutch was provided in a packaged module designed for insertion into S&S Energy Products' LM6000 split skid package between the LM6000 and the generator. Other new equipment installed includes the clutch lube oil system, and a complete re-work of the existing gas turbine control system.
The SSS Clutch is a free-wheel device that enables the LM6000 to be connected and disconnected from the generator automatically. This enables the drive train to go from power generation mode to synchronous condenser mode simply by shutting down the gas turbine.
If the drive train is in power generation mode, and synchronous condensing is required, the fuel to the gas turbine is reduced. Once the gas turbine slows down relative to the generator, which is still connected to the grid, the clutch automatically disengages. If power generation is required while in synchronous condensing mode, the gas turbine is started and accelerated to full power, i.e., 3600 rpm, and the clutch automatically re-engages to transmit power.
With this specially designed clutch, the gas turbine can shut down while the generator remains synchronized to the grid. The unit is capable of supplying or absorbing reactive power. When real power is needed, a signal is sent from the power plant's remote control center and the turbine is started and recoupled to the generator.
The SSS Clutch installed at the Poplar Hill site is the size 260T, a mechanical device that is completely automatic and transmits torque through conservatively rated gear-coupling teeth. The clutch is designed to transmit 52 MW continuously. No external controls or speed sensing devices are required for the clutch. SSS has more than 650 clutches installed in turbo-generator applications, transmitting more than 27 million kW in 55 countries.
The LM6000
The LM6000 shares many of the same characteristics as GE's CF6-80C2 aircraft engine, and is a unique aeroderivative in that its low-pressure turbine can be directly coupled to its load without using a separate power turbine. This concept improves the simple-cycle efficiency, and reduces the gas turbine's cost and unit size.
The LM6000 low-pressure rotor consists of a five-stage low-pressure compressor and a five-stage low-pressure turbine connected by a mid-shaft, which extends through the center of the engine. The high-pressure rotor consists of a 14-stage, high-pressure compressor and a direct-coupled, two-stage high-pressure turbine. Table 2 lists the LM6000s 60-hertz performance specifications.
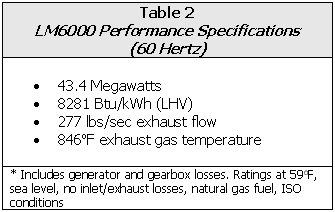
The LM6000 is designed to operate at an output shaft speed of 3600 rpm for electrical power generation. The high-pressure rotor speed varies from ~6000 rpm to 10,600 rpm over the operating power range from idle to full power. A reduction gearbox reduces shaft speed from 3600 rpm to 3000 rpm in 50-Hz applications. The gas turbine is equipped with three systems that control airflow to achieve the desired performance characteristics.
Variable inlet guide vanes in front of the low-pressure compressor modulate airflow entering the flowpath. Variable bleed valves between the low- and high-pressure compressors allow some airflow to be dumped at low power conditions. Six stages of variable stator vanes on the high-pressure compressor stage maintain high efficiency over the power range.
LM6000 Package
S&S Energy Products uses standardized package designs to shorten the manufacturing schedule. This enables S&S Energy to have a power plant operational shortly after the signing of a contract. Packages are factory assembled and tested at full load prior to shipment from the company's Houston headquarters. These tests use the contract control panel and auxiliary systems to minimize field start-up and debugging time. This demonstration of power output and heat rate significantly reduces performance risks for the owner and operator.
Each S&S Energy Products gas turbine package features a UBC Zone 4 earthquake-qualified structural design, durable electrical systems and all stainless steel fluid systems and reservoirs. The Brush generator is designed to accommodate full gas turbine power output over the full ambient air temperature range. The generator is sized larger than the turbine output to accommodate future ratings increases. The gas turbine is controlled by Woodword Governor's NetCon 5000 controls.
PC to PD Replacement
Simultaneous to the clutch installation at the Poplar Hill power plant, S&S Energy Products also replaced the existing LM6000 PC gas turbine with a PD model that features GE's DLE combustion system.
Conclusion
Once the installation of the clutch was complete, and S&S Energy Products performed the gas turbine package modification, the LM6000 began synchronous condensing service Oct. 1, 1999—just 30 days after the unit was brought down for the retrofit. This remotely operated power plant provides support to Alberta's growing grid. With the DLE system in place, the gas turbine also meets Alberta's environmental emissions requirements.
About the author: Thompson graduated from Texas Tech with a mechanical engineering degree and started work at Stewart & Stevenson's gas turbine division in Houston as a mechanical production engineer. After holding positions in applications engineering and sales, Thompson moved to project management following GE's acquisition of the Stewart & Stevenson's gas turbine division—now S&S Energy Products.
Editor's Note: As an internet community for the power generation industry, Power Online strives to bring you the varied voices and viewpoints of professionals from all facets of this field. Be Our Guest is designed for those interested in writing articles or stating their viewpoints about emerging technologies, innovative project financing strategies, power generation industry trends, or sharing problem-solving case studies. If you'd like to be our guest, please send a brief summary of the article or opinion piece to amurelio@verticalnet.com or call 918-749-2648 so we can discuss your idea. ACM