Be Our Guest: Thermoacoustic Engines - Propulsion, Power for the 21st Century

Thermoacoustic engines – What are they?
Thermoacoustics is the term for soundwaves generated by heat. One might accurately say that all heat engines, like those in automobiles and jet planes, generate sound from heat. Internal combustion (IC) engines burn fuel and generate combustion noises that rumble or roar, depending on the type of engine. The noise is a by-product of the engines' energy conversion process. Fuel is mixed with air and burned to produce hot, expanding gases that drive pistons and turbines directly.
A Thermo-Acoustic Cycle (TAC) engine, however, is a different animal altogether. The usual arrangement consists of a closed, resonant chamber containing three heat exchangers and a working fluid—generally an inert gas under pressure. Heat is injected from outside the resonator, into the internal working fluid, via the hot-side heat exchanger (HXh), causing an increase in pressure. At the other end the resonator, a coolant circulating through the cold-side heat exchanger (HXc) removes the heat energy from the working fluid, causing a reduction in pressure.
In accordance with Boyle's and Charles' Laws, a confined gas will increase in pressure by 1/273rd for each degree of increase in Celsius temperature. If the resonator cavity is pressurized to twenty atmospheres static pressure to begin with (Ps), and the temperature of the gas is increased by 600 Co, the peak dynamic pressure (Pd) will be:
Pd = 20 atm / 273 * 600 + 20 atm
Pd = 64 atm
Neglecting gas losses and thermal reactance in the materials of the resonator, the dynamic swing in pressure will be:
The third heat exchanger is usually located somewhere between HXh and HXc, and is a passive device commonly referred to as a "regenerator". This is a colloquial term, though still in common use, and the correct designation for it is "thermal capacitor" (Ct). Ct is the heart of the TAC engine. It acts something like a transistor oscillator, in that it teeters back and forth thermally, taking up energy from the working fluid, then giving it back, thereby keeping the oscillation going. The timing of this periodic "push" is normally accomplished through geometry, i.e., the physical location of Ct is ninety degrees removed from HXh with respect to the wavelength, or cycle, of the resonator, but the phase difference can also be accomplished by tailoring the thermal mass of Ct to conduct thermal energy at a specific rate. This permits resonator design variations not restricted by a set geometry. Energy acquisition and decay in Ct is illustrated below:
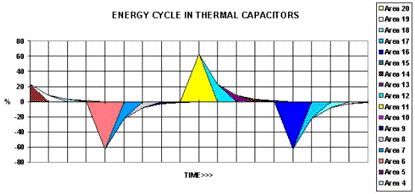
Once the speed of the cycle (hundreds to thousands of Hertz) is taken into account, it is easy to understand how the engine produces useful power. Thermal energy migrates through the working fluid from HXh to HXc in the form of a rapidly moving wavefront, a pressure wave, or shockwave. This is the acoustic component, a pressure wave moving through an elastic medium. Lightning is a good analogy. An electric arc cutting through the atmosphere superheats a channel of air, and the resulting explosive expansion of atmospheric gases produces a shockwave that is commonly called a thunderclap. The traveling acoustic pressure wave carries with it the thermal component that produced the wave. In other words, it transports the heat of the lightning bolt, diffusing it to the surrounding atmosphere.
A similar phenomenon takes place inside a TAC engine. Like water in a wavepool, the acoustic pressure wave sloshes back and forth inside the resonant cavity, being alternately heated and cooled, the pressure component ballooning and contracting repeatedly. The result is a resonator, or engine, with a rapidly fluctuating pressure gradient and no moving parts. This oscillating pressure gradient can be tapped off to drive a piston, and a linear alternator that produces electricity.
For example, a pressure swing of 44 atm (45 kg/cm2) is a significant force, and when it occurs five hundred times per second, the potential power output is quite high. For example, at this dynamic pressure, a piston of ten square centimeters surface area (1.5 square inches), with a travel of only one centimeter (0.4 inch), operating at a frequency of five hundred Hz, will produce:
Extraordinary performance, from a piston the size of a coin.
The TAC engine is attractive for several reasons. If an external piston or alternator shaft is not counted, it has no moving parts to wear out and the overall part count is low, meaning low manufacturing costs. The engine can be adapted to operate over a wide temperature range, so energy recovery from waste heat in industrial processes and cogeneration power plants, and even power generation from resources such as solar energy and moderate thermoclines in lakes and brine ponds, becomes economically viable.
The TAC engine is a Carnot engine, in that overall efficiency is governed primarily by the temperature delta across its isothermal heat exchangers, HXh and HXc, i.e.:
Low production costs mean that lower operating efficiencies can be tolerated. Because efficiency is not necessarily a barrier, TAC engines may also fill low temperature niches that are problematic for other power sources. Fellows Research Group of Austin, TX (FRG), for instance, anticipates low temperature biomedical applications in which miniaturized TAC engines will generate power for medical prostheses from body heat, at single-digit efficiencies. These microminiature TAC engines are called TARs, for Thermo-Acoustic Resonators. Hearing aids, pacemakers, baby crib monitors, personal security alarms for women and children, physiological monitors for policemen, firemen, soldiers and hospital outpatients, in the form of a ring or wristwatch, will all operate indefinitely, and without batteries, acquiring energy through contact with the body. Since they will never require maintenance, they may even be implanted permanently inside the body. One configuration of these micro-chip size devices is illustrated below:
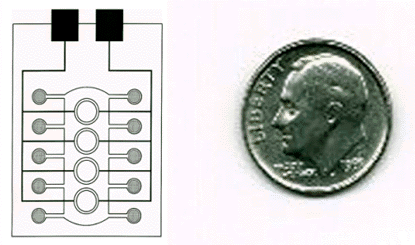
The center array is comprised of linear alternators, flanked by miniature heat exchangers.
Applications are almost limitless. The heat generated by the CPU in a laptop computer can be used to recharge the battery, extending operating time between charges. Automobile exhaust heat can be used to charge the vehicle battery, doing away with the alternator and reducing fuel consumption and air pollution. Passenger planes can generate power for aircraft systems from waste engine heat, saving fuel. Pets and wildlife can be monitored via TAR-powered locator beacons.
About the author: Lee Fellows is general manager and vice-president of Fellows Research Group (FRG), an applied research firm in Austin, TX. Fellows formed FRG with his wife in 1993, after a 21-year career as a chief of operations (civil engineers) in the U.S. Air Force, and as a facilities manager in several United States national parks. Fellows also writes adventure novels under the name Oscar L. Fellows. More information on TARs and TAC engines can be found on FRG's website at: http://www.io.com/~frg, or you can e-mail FRG at frg@io.com. Copyright 2000 by Oscar L. Fellows.
Editor's Note: As an Internet community for the power generation industry, Power Online strives to bring you the varied voices and viewpoints of professionals from all facets of this field. Be Our Guest is designed for those interested in writing articles or stating their viewpoints about emerging technologies, innovative project financing strategies, power generation industry trends, or sharing problem-solving case studies. If you'd like to be our guest, please send a brief summary of the article or opinion piece to amurelio@verticalnet.com or call 918-749-2648 so we can discuss your idea. ACM